Project Overview
A major global manufacturer of cab HVAC systems for Class 8 truck and construction/agriculture equipment was challenged by its customers to develop the next generation system for a new product launch. Two objectives of the new system were to develop a more efficient blower assembly that produced lower audible noise. TEC AIR was the natural partner for this blower development project. TEC AIR was a long time supplier to the HVAC system supplier. Coupling the prior relationship and TEC AIR's 50+ years of experience in designing and manufacturing efficient, low noise blower assemblies was a win-win solution.
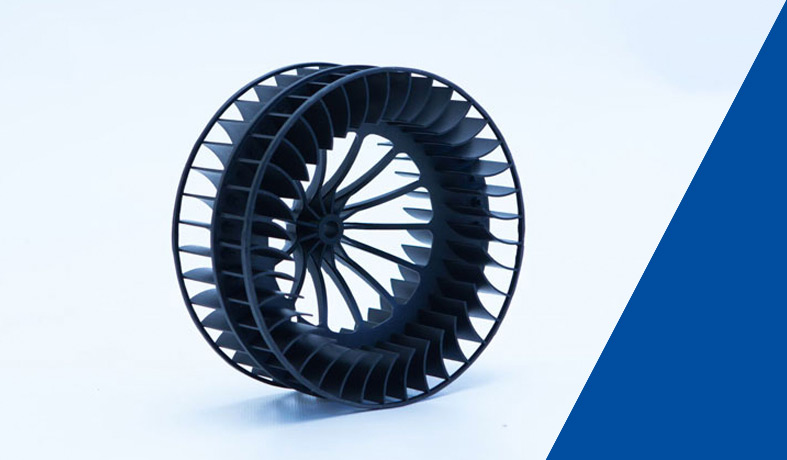
The Challenge
Challenged to come up with a better blower assembly, a global HVAC system provider searched its portfolio of options and came up with two solutions - neither of which met the customer's needs. One was a low cost, high output, high noise and low efficiency blower assembly using an Asian motor and plastic blower wheels and scrolls. The second was a high cost, low output, low noise, higher efficiency blower assembly purchased as an assembly from Europe. TEC AIR's challenge was to redesign the blower wheel and scroll to match the high output and high efficiency while also achieving the low noise and the low cost - that is, essentially to have the best of both units in one new blower assembly.
The Solution
TEC AIR began by redesigning the blower wheel. By redesigning the blower, TEC AIR was able to improve the efficiency of the blower assembly and reduce both blade pass frequency noise and overall air rush noise. Utilization of leading edge blade effects, asymmetrical blade spacing, tuning of the number of blades and their chord angles and lengths resulted in partial achievement of the customer objective. TEC AIR then turned to the scroll design for further improvement. Redesign of the scroll evolution and the scroll cutoff yielded significant improvement in efficiency and reduction in blower noise. Finally, TEC AIR provided direction to the electric motor manufacturer to tune the motor for optimal RPM and efficiency to ultimately achieve the desired airflow and efficiency. TEC AIR fabricated prototype blower wheels and scrolls to test airflow, efficiency and sound in TEC AIR's engineering labs to validate the new design.
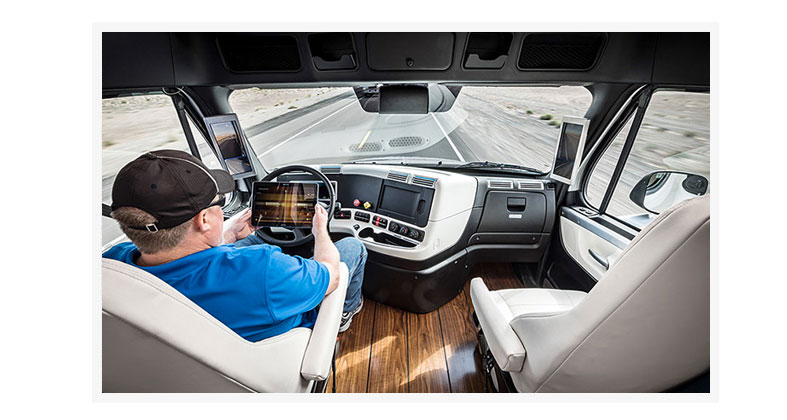
Final Outcome
Maximum airflow, low noise and highly efficient blower assemblies at a cost competitive price are common place demands in the automotive, heavy truck and off-road markets. Rapid development of new blowers and the ability to simulate results in CAE and validate new designs in the lab are an integral part of TEC AIR's supply chain value proposition. In this case, TEC AIR developed a solution that provided both the maximum airflow and low cost of one blower assembly and the low noise and efficiency of a second assembly meeting the customer need. Prototype parts and ultimately production tooling were developed to support the commercialization of this new blower.